Thermoplastic Powder for Dipping Purposes
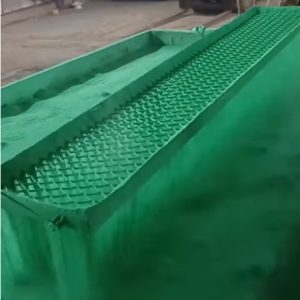
Introduction of thermoplastic powder for dipping purposes
Thermoplastic powder for dipping purposes is a type of powder coating material that is used to provide a protective and decorative coating to various objects. The coating is applied through a dipping process, where the object is immersed in a container filled with the thermoplastic powder. The powder particles adhere to the surface of the object, forming a uniform and continuous coating.
The thermoplastic powder is typically made from a polymer resin, which can be melted and re-solidified multiple times without undergoing any significant chemical change. This characteristic allows the powder to be heated and melted onto the surface of the object during the dipping process. Once cooled, the powder forms a solid and protective coating.
Dipping Process
The thermoplastic powder dipping process involves several steps. First, the object is cleaned and pre-treated to remove any dirt, grease, or other contaminants that may interfere with the adhesion of the powder. The pre-treatment may involve washing, degreasing, or sandblasting, depending on the type of object and the desired coating properties.
Next, the object is heated to a specific temperature, usually between 250°C and 330°C, to ensure that the surface is dry and free of any moisture. The object is then immersed in a container filled with the thermoplastic powder. The container is a fluidized bed.
In a fluidized bed, the powder particles are suspended in a stream of air, creating a fluid-like bed. The object is immersed in the bed, and the powder particles adhere to the surface due to the fluidizing action.
After the object is removed from the powder container, excess powder is usually removed through shaking or air blowing. The coated object is then subjected to a curing process, which involves heating the object to a specific temperature for a specific time. During this process, the thermoplastic powder melts and flows, forming a continuous and uniform coating. Once cooled, the coating hardens and provides excellent protection against wear, chemicals, and UV radiation.
Advantages
Thermoplastic powder coatings offer several advantages over other coating methods. They have a lower environmental impact as they do not contain volatile organic compounds (VOCs) and can be easily recycled. They also provide a wide range of colors, allowing for customization and aesthetic appeal.
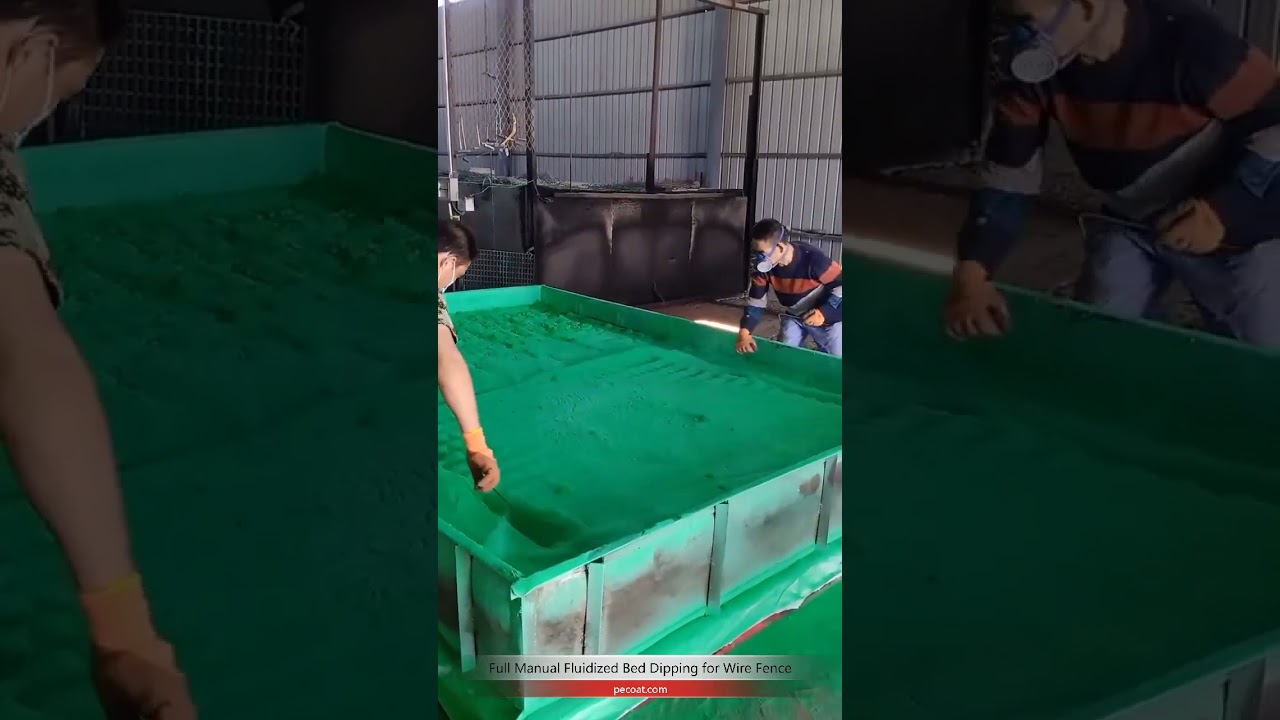
In summary, thermoplastic powder for dipping purposes is a versatile and durable coating material that can be applied through a dipping process. It offers excellent adhesion, durability, and corrosion resistance properties, making it suitable for various industries. The dipping process involves several steps, including pre-treatment, heating, immersion, and curing. Thermoplastic powder coatings offer several advantages over other coating methods, including lower environmental impact and customization options.