Automatic Fluidized Bed Dip Powder Coat Line for Refrigerator Grids Shelves
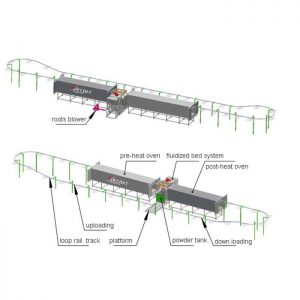
Design Consideration
- Maximum workpiece size: 1005×577×40mm
- Normal workpiece size: 300×500×10 mm
- Heating source: Electricity
- Equipment footprint area: 25meter×9meter, high 3.5meter
- Equipment Type: Automatic type
Production Output:
- 1005×577×40mm : 200pcs/hour
- 300×500×10mm: 500 pcs/hour
Work-pieces To Be Coated
Specifications for Equipment
- Maximum work-piece size: 1500×600×10mm,
- Normal work-piece size: 300x500x10mm
- Output capacity: 320 pcs/hour
- Hanging tray size: 1600mm×600mm
- Size of preheat oven: 13m*1m*1.2m
- Size of post-heat oven: 10m*1m*1.2m
- Maximum temperature of preheat oven: 400℃
- Maximum temperature of post-heat oven: 400℃
- Voltage: 380V 50HZ
- Pressure of compressed air: 0.6Mpa
- Footprint area of whole equipment: 46m*8m, high 3.5m
- Numbers of operation person: total 7
Design & Drawings
Operation Procedure
- Check and make sure all parts are ready for running: the temperature in both oven has raised to specified value; the powder tank is filled with powder, and in boiling state.
- At uploading area, workers start to hang the work-piece on the hanging tray.
- Turn on the line, the loop rail track send the work-piece to pre-heat oven.
- Workers continue upload work-piece
- After preheating, work-piece enter into fluidized bed system to dip powder
- After dipping powder, the fluidized bed go down, meanwhile it shake off the extra powder
- The loop rail track continue going
- The work-piece enter into post-heat oven for curing and leveling.
- Workers download the work-piece after it goes out of post-heat oven
- Next loop start
Comments are Closed