Flame Spray Thermoplastic Powder for Steel, Wood and Concrete
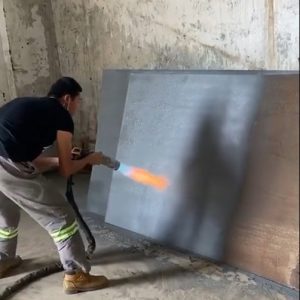
Thermoplastic powder flame spray is a process where plastic powder is heated to a molten or semi-molten state using the heat generated by the combustion of fuel gas (such as acetylene, hydrogen, natural gas) and oxidizing gas (oxygen, air) in a specially designed spray gun. The heated powder is then sprayed onto the pre-treated surface of the workpiece under the action of a carrier gas (usually compressed air), and the droplets flow and flatten to form a coating. The main process parameters for spraying include the flow rates of fuel gas and oxidizing gas, spraying distance, preheating temperature of the workpiece, and airflow.
By using flame spraying technology, various performance coatings such as corrosion resistance, wear resistance, and friction reduction can be obtained. The flame spray thermoplastic powder can be a single plastic powder or a resin-modified powder, or a composite powder that mixes metal, ceramic, and plastic powders to improve coating performance. Experiments have shown that adding 5% to 30% volume of Fe-Ni-B alloy powder to high-density polyethylene powder (HDPE) can significantly improve the wear resistance, thermal conductivity, and load-bearing capacity of the sprayed coating. Under sliding friction without lubricant, the coating friction coefficient is reduced by 1.2 to 1.5 times, and the relative wear resistance is increased by 7.3 to 18 times. Adding 5% to 10% volume of powder solid lubricant reduces the coating friction coefficient from 0.38 to 0.19. The friction coefficient is reduced even more when lubricant is present.
Currently, thermoplastic powder flame spraying technology has been applied in industries such as chemical, textile, and food machinery, playing a role in corrosion resistance, friction reduction, and wear resistance.
Flame Spray Thermoplastic Powder Coating for Steel, Wood and Concrete
PECOAT® flame spray thermoplastic powder is based on acid modified polyolefins,formulated with various additive to provide a tough long lasting coating on outdoor structures made of steel, aluminum,wood and concrete,etc. The coating maintains excellent adhesion to the substrate and provides a good degree of electrical insulation, abrasion and impact resistance.
TYPICAL USES
Corrosion protection. Application on-site on large structures either fixed or hard to disassemble which are submitted to adverse weather conditions, salt spray and typical airborne pollutants, chemical corrosion.
TYPICAL PROPERTIES OF THE POWDER
- Coverage (100% efficiency): 3.5m2/Kg at 400 microns
- Particle Size: 95% less than 250 microns
- Bulk Density (at rest): 0.37 g/cm3
- Fluidising Characteristics: Excellent
- Packaging :25 kg cardboard boxes
STORAGE
Flame Spray Thermoplastic Powder is stored in a clean dry area at 10-25°C and out of sunlight, the material should not deteriorate. However, in the interest of good housekeeping, old stocks should be used first.

Why use Thermal Flame Spray Thermoplastic Coatings?
Thermal Flame Spray thermoplastic Coatings are commonly referred to as “thermoplastics”, Melt on heating and re-solidify on cooling. Common plastics are polyethylene, polystyrene, polypropylene, nylon, PVC etc. Range of properties-from flexible to rigid, high temperature or chemical resistance, toughness, electrical insulation etc. On heating, they react with themselves to “cross-link” the molecules into a matrix which solidifies and will not melt again on reheating.
- Good resistance to stress cracking, adverse weather conditions, detergents, salt and typical airborne pollutants
- Excellent adhesion
- Excellent abrasion and impact resistance
- Superior chemical resistance
- UV rays resistance
- Flexibility and Repairability
- Anti-osmotic barrier
- Halogen free
- Combustion fumes are low in smoke
- Low toxicity index
- Environmentally safe
I use this thermal flame spray powder for my swimming pool,I buy 20KG,write to me,thanks
you’re really a good webmaster. The site loading speed is amazing. It seems that you are doing any unique trick. In addition, The contents are masterpiece. you’ve done a excellent job on this topic!