Electrostatic Spray Thermoplastic Powder Coating
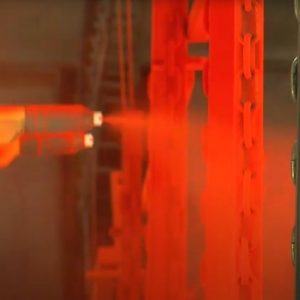
PECOAT® Electrostatic spray thermoplastic powder coating is a thermoplastic powder prepared from polyethylene resin, compatibilizer, functional additives, pigments and fillers. It has excellent adhesion and anti-corrosive properties, as well as good chemical stability, electrical insulation and low temperature resistance. It can be designed according to customer requirements. Compared with ordinary PE powder coating, its main feature is thin coating, which can be sprayed in both cold work-piece and preheated work-piece. It is also suitable for fluidized bed dipping process.
Characteristics
- Various use method: electrostatic spray, fluidized bed dip, blockspaying
- Thin coating ,Smaller particle size
- Suitable for cold workpiece and preheated workpiece
Use
Various types of chemical equipment, industrial pipelines, and metal components. It is especially effective for complex work-pieces.
Use Method for electrostatic spray thermoplastic powder coating
1.Fluidized Bed
For fluidized-bed dipping, preheat parts to 230°C adjusting for part thickness. Dip parts in fluidized-bed for 8-10 seconds. Allow excess powder to stand for 1 minute then carefully blow off the excess material. Post-heat at 193 – 205°C for 3 – 4 minutes.
2.Electrostatic Deposition
PECOAT® Electrostatic spray thermoplastic polyethylene powder coating can be applied via electrostatic deposition with or without pre-heat.
- When not using pre-heat, the powder should be applied to achieve a thickness 203 – 254µm. Recommended voltage setting when using Corona equipment is 40 – 60 kv. Post-heating at 175 – 220°C for 5 to 10 minutes depending on metal thickness, or until desired flow out is achieved.
- For preheated parts, the recommended preheat temperature is 205°C. Deposit 203 – 300µm or higher if desired. For improved surface finish, parts may be post-heated for a short period of time if necessary. Times and temperatures in the oven will depend on configuration and thickness of the part.
Powder Properties for electrostatic spray thermoplastic powder coating
- Specific Gravity: 0.91-0.95 (vary with colors)
- Nonvolatile matter: ≥99.5%
- Melt flow index: 5-50g/10minutes (2.16kg, 190℃)
- Particle size: suitable for electrostatic spraying and in fluid bed .
Coating Properties
Parameters conditions: Steel plate with 2mm thickness, surface degreasing and rust removal, coated under standard conditions, coating thickness 400um.
- Coating thickness(GB/T1764): 150μm- 400μm
- Appearance: Flat and smooth ( slight orange peel allowed)
- Gloss (GB9754, 60°): 10-75(adjusted according to customer requirements)
- Shore hardness(D) (GB2411): 44-55
- Low temperature resistance Q/HJ 008-2008: No crack at -35℃,60h
- Bending (GB6742): ≤2mm (at thickness 200um)
- Impact test (9N·m) GB/T18226: The coating does not flake or break
- Vicat softening point (GB1633): 70-75℃
- Salt Spray Resistance -500h no cross-cut( GB/T 18226) : No blistering, peeling and rusting; -8h Cross-cut (GB/T 18226 ): No blistering, peeling and rusting
- Humidity and Heat Resistance(8h GB/T 1740): No blistering, peeling and rusting
- Weather Resistance
-Manual acceleration 1000h(GB/T 1865): Loss of light, discolor: 1 level; Chips, Rrack: 0 grade
-Natural exposure for one year(GB/T9276): Loss of light, discolor: 1 level; Chips, Crack: 0 grade - Soak in 5%Hcl for 400h: No change in coating
- Soak in 5%NaOH for 72h: No change in coating
Packing and Storage for electrostatic spray thermoplastic powder
25kg/bag,Stored in a clean dry area less than 40℃ and out of sunlight , storage time 2 years. After expiration, it can still be used if no quality problem after testing. PECOAT® Electrostatic spray thermoplastic powder coating can not be mixed with powder from other supplier.
Health and safety
PECOAT® Electrostatic spray thermoplastic powder coating is non-toxic and harmless. However, dust inhalation should be avoided during use. It is recommended that operators wear appropriate dust masks and glasses. If possible, try to avoid prolonged skin contact with the powder.

hello,what is the particle size of this electrostatic grade?
how much for this electrostatic spraying powder?