Dip Powder Coating And Spray Powder Coating
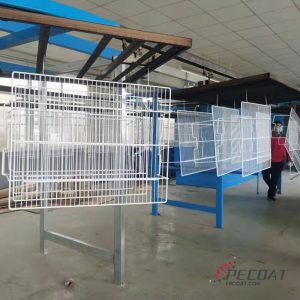
1. Different concepts
1) Spray Powder coating:
Spray Powder coating is a surface treatment method that involves spraying powder onto a product. The powder usually refers to thermosetting powder coating. The surface of powder-coated products is harder and smoother than that of dip-coated products. Electrostatic generators are used to charge the powder, which is then attracted to the surface of the metal plate. After baking at 180-220℃, the powder melts and adheres to the metal surface. Powder-coated products are often used for indoor use, and the paint film has a flat or matte or art effect.
2) Dip powder coatings:
Dip powder coating involves heating metal and evenly coating it with plastic powder to form a plastic film, or heating and dipping the metal into a dip coating solution to cool and form a plastic film on the metal surface. The powder usually refers to thermoplastic powder coating. Dip coating can be divided into hot dip coating and cold dip coating, depending on whether heating is required, and liquid dip coating and powder dip coating, depending on the raw materials used.
2. Different processing methods
1) There are various types of spray powder coating, such as acrylic powder, polyester powder, and epoxy polyester powder. Spray powder coating has higher product quality and weight than dip powder coating, but the product surface is good and smooth for both methods.
2) Dip coating is cheaper than spray powder coating because the price of dip coating powder is lower than that of iron. Dip powder coating has the advantages of anti-corrosion and rust prevention, acid and alkali resistance, moisture resistance, insulation, good touch, environmental protection, and long service life. Dip coating thickness is generally thicker than spray powder coating, with a thickness of over 400 microns compared to 50-200 microns for spray powder coating.
1) Dip coating powders:
①Civil powder coating: mainly used for coating clothing racks, bicycles, baskets, kitchen utensils, etc. They have good flow, gloss, and durability.
②Engineering powder coating: used for coating highway and railway guardrails, municipal engineering, instruments and meters, supermarket grids, shelves in refrigerators, cables, and miscellaneous items, etc. They have strong durability and corrosion resistance.
2) Dip coating principle:
Dip coating is a heating process that involves preheating metal, dipping it in a coating solution, and curing it. During dipping, the heated metal sticks to the surrounding material. The hotter the metal, the longer the dipping time, and the thicker the coating. The temperature and shape of the coating solution determine the amount of plasticizer that sticks to the metal. Dip coating can create amazing shapes. The actual process involves adding powder coating to a bottom porous container (flow tank), which is then agitated by compressed air treated by a blower to achieve a “fluidized state”, forming a uniformly distributed fine powder.
3. Similarities
Both are surface treatment methods. The colors of both methods can be yellow, red, white, blue, green, and black.
Please tell me more about this. May I ask you a question?