An Overview of Dip Coating and Dip Molding
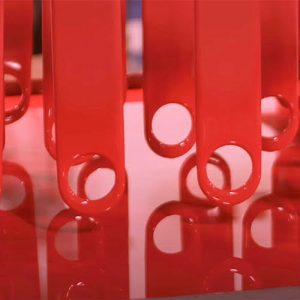
Process of Dip Coating and Dip Molding
Dip Coating
The process of fusing a plastic material onto a pre-existing metal piece is known as dip coating. The metal to be coated serves as a mold, allowing the plastic or polymer to adhere to it during the process. Prior to dipping, the parts (and sometimes entire pieces) intended for dipping are treated and preheated before being directly placed into the liquid polymer (e.g. PVC plastisol ). Upon cooling, the liquid polymer adheres to the metal and solidifies, resulting in a thick plastic coating surface that offers both protective and decorative properties. This enhanced surface provides increased resistance against scratches, wear, corrosion, and external factors while also improving durability and extending service life of metal parts. Dip coating not only offers convenience but also ensures user safety by providing an insulating surface with improved grip.
Common applications of dip coatings include hand tools such as pliers which benefit from their ability to compress or bend rigid materials while preserving tool integrity after applying a plastic coating on handles. Additionally, dip coatings find utility in various other products like shopping carts, baskets, tweezers, lids, hats, stoppers etc., where rigidity is desired.
Furthermore, plastic coatings serve as effective thermal and electrical insulators offering additional protection when handling hot objects in hand tools like pliers and shovels; they can also be utilized for insulation purposes in electronic components such as wires,cables,and digital instrument probes.
Dip Molding
The process of dip molding is similar to that of dip coating, with the addition of a demoulding or unloading step. Dip molding allows for the production of single wall, hollow, and double wall parts, eliminating the need for subsequent processes such as trimming and deburring. This results in raw material savings due to reduced secondary operations. Examples of plastic products manufactured through this process include latex gloves, fashion and apparel accessories, cups, plastic lids, and entertainment equipment parts.
Type of Dip coating and Molding Polymer
The most commonly utilized polymers for coating materials include plastisol, latex, neoprene, polyurethane, and epoxy. An important characteristic of these polymers is their ability to be readily available in liquid form at room temperature without requiring additional processing. Moreover, prior to considering the use of the liquid polymer in dip coating and dip molding processes, it must possess sufficient viscosity to prevent excessive runoff from the mold surface. Consequently, the polymer settles onto the surface until it undergoes curing.
Plastisol
Plastisol, the most commonly utilized polymer in dip molding and dip coating processes, consists of finely dispersed polyvinyl chloride (PVC) resin within a liquid plasticizer. Upon heating, it solidifies and subsequently cools into a soft, elastic material with rubber-like properties. Renowned for its exceptional toughness, corrosion resistance, and impact resistance, Plastisol coatings are particularly suitable for electrical applications due to their high dielectric strength. Additionally, colorants can be incorporated to customize the final product’s appearance.
Latex
The emulsion of latex consists of small polymer particles, with rubber particles accounting for 30-40% of the total. It serves as a crucial raw material in rubber production and can be either natural or synthetic. The polymer is easily accessible and poses no toxicity concerns. However, certain studies suggest that when it degrades into powder form, some individuals may experience allergic reactions, leading to a decline in its popularity.
Neoprene
Neoprene is made from the polymerization of neoprene rubber and is an alternative to latex. It is known for its chemical resistance and flexibility.
Polyurethanes
Polyurethanes are composed of carbamate (or ethyl carbamate) groups linked by carbamate. It is known for its flexibility and high elasticity to deformation.
Epoxy
Epoxy is a thermosetting polymer that, once the polymer chains are cross-linked, forms a coating of high strength, chemical and heat resistance.