Why Use a Release Agent?
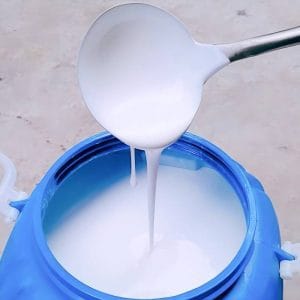
A release agent is a substance applied to molds (molds, dies, or surfaces ) to prevent materials being molded (e.g., plastics, rubber, metal, composites, or concrete) from sticking to the surface, ensuring easy removal of the finished product. Here are the key reasons for using release agents:
1.Prevent Adhesion Between Product and Mold
- During manufacturing processes (e.g., injection molding, casting, thermoset curing, or composite layup), the material in its molten, liquid, or semi-solid state can bond to the mold surface due to molecular forces (e.g., van der Waals forces) or chemical reactions (e.g., cross-linking in rubber or resin curing).
- Release agents create a thin, non-stick barrier between the material and the mold, breaking this adhesion and allowing the product to be removed intact without tearing, fracturing, or leaving residue.
2.Protect the Mold Surface
- Repeated contact and removal of molded products can cause abrasion, scratches, or chemical corrosion on the mold surface (e.g., high-temperature oxidation in metal casting or additive migration in plastic molding).
- A release agent reduces friction and wear, extending the lifespan of expensive molds and minimizing maintenance or replacement costs.
3.Enhance Production Efficiency
- Without a release agent, stuck products can lead to frequent mold cleaning, downtime for repairs, or manual intervention to pry parts free—all of which slow down production.
- Release agents enable smooth, automated demolding, reducing cycle times and increasing output, especially in high-volume manufacturing.
4.Improve Product Surface Quality
- Adhesion issues can cause surface defects like scratches, tears, or incomplete demould (e.g., “mold release failure” in plastics, where part of the product remains in the mold).
- A release agent ensures the product maintains its intended shape and surface finish, which is critical for applications requiring high precision (e.g., automotive components, medical devices) or aesthetic appeal.
5.Reduce Costs
- By minimizing scrap rates, mold damage, and labor for rework or cleaning, release agents lower overall production costs.
- Their use is particularly cost-effective for complex or large molds, where mold downtime and repair expenses are significant.
6.Facilitate Post-Processing
- Some release agents leave no residue or interfere minimally with post-molding operations like painting, welding, bonding, or electroplating—ensuring compatibility with downstream processes.
In industries ranging from plastics and rubber to metalworking and construction, release agents are essential for achieving efficient, high-quality manufacturing by balancing mold protection, product integrity, and cost-effectiveness. The choice of release agent depends on factors like molding temperature, material type, mold design, and desired surface properties, with options including wax-based, silicone-based, fluoropolymer, or water-based formulations.