This dip mould machine is used for producing PVC end caps, sleeves and covers by plastisol dipping mould technology. Designed and manufactured by the PECOAT® machinery team, it is a highly automated dip molding equipment integrating processes like dip molding, curing, demolding, timing and temperature control. The production process needs no manual intervention. The machine body is welded with stainless steel and iron. The track tray employs a servo motor for precise positioning. The oven is heated by electric furnace wires. The equipment is equipped with three-color normal and abnormal warning lights, leakage and power failure safety protection functions and related safety protectors.
Relevant Components and Production Processes
The entire production process consists of the following steps:
- Preheating: The mold enters the oven for preheating at 220-250℃ for 2-5 minutes.
- Dipping: Dip the mold into the PVC plastisol so that the plastisol sticks to the mold.
- Curing: The mold enters the oven again for leveling and curing.
- Cooling: Dip the mold into water for cooling.
- Automatic demolding: Demold through air spraying. (Note: Special-shaped products cannot be automatically demolded and need manual blowing assistance.)
- Dipping release agent: After demolding, the mold dips in the release agent and enters the next cycle.
The entire process is largely automated and does not require manual operation. Only a patrol is needed every 30 to 40 minutes to add plastisol materials.
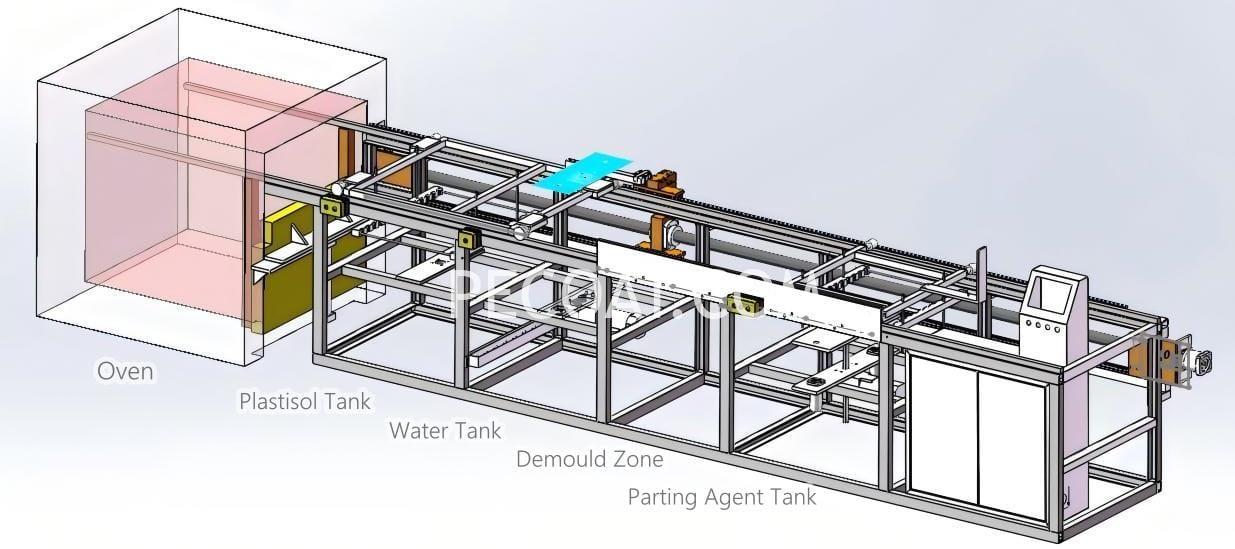
Specification
Description | Details |
---|---|
Machine type | Fully automatic |
Machine size | Length 5330 mm, width 1200 mm, height 1100 mm |
Output per cycle | 3 - 4 minutes for one mold base plate |
Number of molds per mold base plate | 200 - 300 pcs (The larger the size of the mold is, the fewer the number of molds that can be hung on the mold base plate will be)) |
Material | Stainless steel and iron welding |
Voltage | According to the customer's country regulations |
Leakage Current Power-Off Protection Function | Yes |
Total power of equipment | 30kw |
Operator required | Unattended, just patrol every 30 - 40 minutes and add materials. |
Production time | 20-25 days |
PLC Control | Yes |
Items to be prepared by the buyer | 1. PVC plastisol (PECOAT® is optional) |
2. Release agent (PECOAT® is optional) | |
3. Mold (customization service can be supplied) | |
4. 5.5kw screw compressor (recommended) | |
5. 1 cubic air storage tank (recommended, suggested) |
Video Demonstration






Tony –
What price please write to me