Physical Modification of Polypropylene
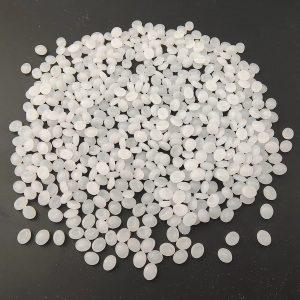
Adding organic or inorganic additives to the PP (polypropylene) matrix during the mixing and compounding process to obtain high-performance PP composite materials. The main methods include filling modification and blending modification.
Filling modification
In the PP molding process, fillers such as silicates, calcium carbonate, silica, cellulose, and glass fibers are added to the polymer to improve heat resistance, reduce costs, increase rigidity, and reduce molding shrinkage of PP. However, the impact strength and elongation of PP will decrease. Glass fiber, as an excellent inorganic non-metallic whisker, has low price, good insulation, heat resistance, corrosion resistance, and high mechanical strength. It is widely used, and the performance of PP modified by glass fiber filling is significantly improved. However, when the glass fiber content reaches about 30%, the mechanical properties of the material can be significantly improved. Excessive addition of glass fiber can result in insufficient impregnation of some glass fibers, leading to poor bonding performance between the polymer matrix and glass fibers, resulting in a decrease in the mechanical strength of the composite material. Moreover, as the glass fiber content increases, the flowability of the composite material decreases, leading to difficulties in PP molding and processing.
Blending modification
Blending PP (polypropylene) with polyethylene, engineering plastics, thermoplastic elastomers or rubber to improve the performance of PP. Blending modification is completed in processing equipment such as internal mixers, open mills, and extruders. The process is easy to control, has a short production cycle, and low cost, and can improve various properties of PP such as colorability, processability, antistatic properties, and impact resistance. Polymer blending can comprehensively utilize the outstanding properties of each component, make up for the shortcomings of each component’s properties, and significantly improve the comprehensive performance of the blend. However, the low-temperature resistance and aging resistance of blended PP are still not ideal. During blending modification, shear force may cause some large molecular chains to be cut and form free radicals, which can form graft or block copolymers and effectively act as compatibilizers for PP.
PP modification technology has greatly expanded the application field of composite materials and improved the cost-effectiveness of products, promoted the engineering process of PP, and expanded its application range from general plastics to engineering plastics. In recent years, the research and development of PP modification technology has developed rapidly, and more and more new technologies have been applied to PP modification, which has significantly improved the comprehensive performance of PP and continuously expanded its application field, with broad development prospects.
Reinforcement modification
Adding fibrous materials to plastics can significantly improve the strength of plastic materials, hence the name reinforcement modification. Materials with a large diameter-to-thickness ratio can significantly improve the bending modulus (rigidity) of plastic materials, which can also be called reinforcement modification.
The reinforcement materials mainly used in the reinforcement modification of PP (polypropylene) are glass fiber and its products, as well as carbon fiber, organic fiber, boron fiber, whiskers, etc. Among them, the glass fibers used in glass fiber reinforced PP are mostly non-alkali glass fibers and medium-alkali glass fibers, with non-alkali glass fibers having the largest amount. The diameter of glass fibers is controlled within the range of 6-15μm, and the length of glass fibers must be guaranteed to be within 0.25-0.76mm, which can ensure the performance of the product and make the glass fibers well dispersed.
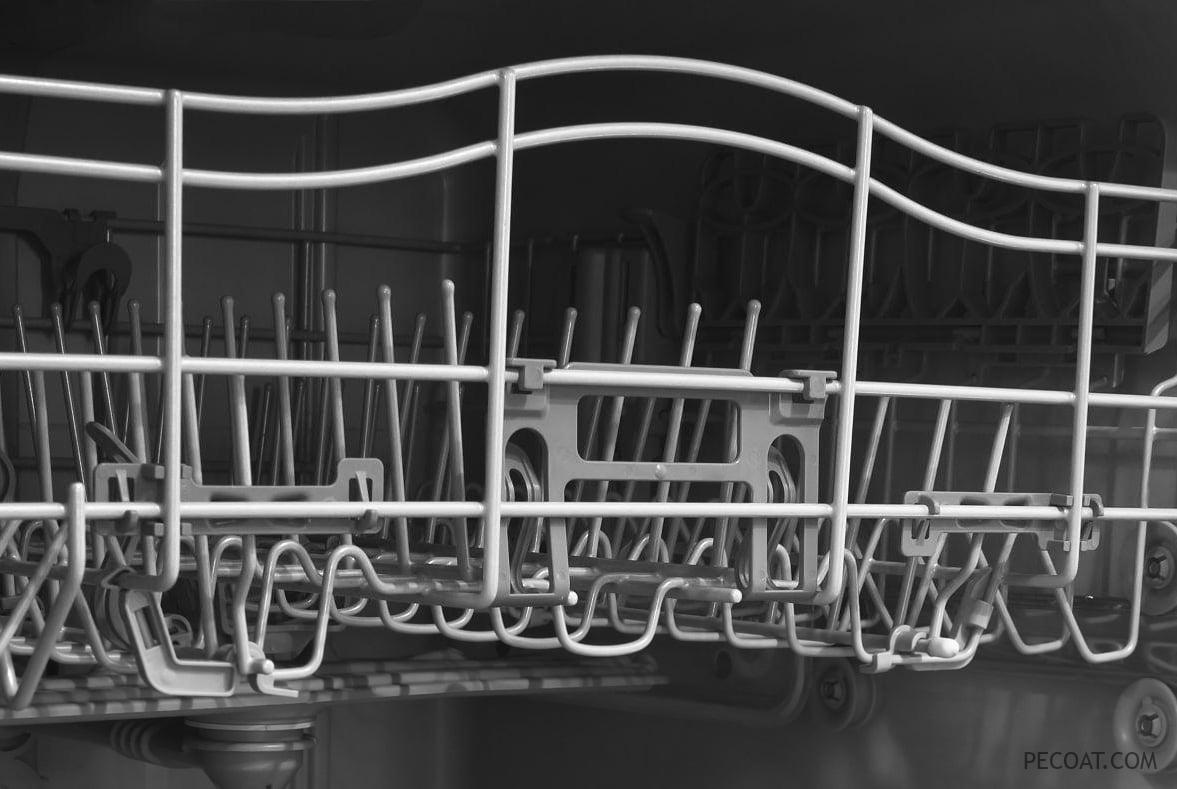
It is generally believed that the length of glass fibers in the product should be greater than 0.2mm to have a modification effect. The glass fiber content (mass fraction) is best between 10% and 30%, and the performance decreases when it exceeds 40%. In addition, adding organosilane coupling agents can make glass fibers and PP form a good interface, improve the bending modulus, hardness, load deformation temperature, and especially dimensional stability of the composite system. Glass fiber reinforced PP can improve mechanical strength and heat resistance, and its resistance to water vapor, chemical corrosion, and creep is also good. It can be used as engineering plastics in many occasions, such as fan blades, heater grilles, impellers, lampshades, electric furnaces, and heater housings, etc.
While the production of polypropylene is rapidly increasing, its performance is also constantly improving, making its application breadth and depth constantly changing. In recent years, some new polypropylene varieties with unique properties have emerged, such as transparent polypropylene and high-melt-strength polypropylene, either through improvements in the polymerization reaction or measures taken during the granulation after polymerization.