Nylon Powder Uses
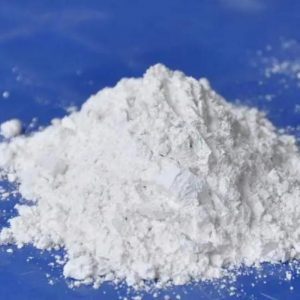
Nylon powder uses
Performance
Nylon is a tough angular translucent or milky white crystalline resin. The molecular weight of nylon as an engineering plastic is generally 15,000-30,000. Nylon has high mechanical strength, high softening point, heat resistance, low friction coefficient, wear resistance, self-lubrication, shock absorption and noise reduction, oil resistance, weak acid resistance, alkali resistance and general solvents, good electrical insulation, has Self-extinguishing, non-toxic, odorless, good weather resistance, poor dyeing. The disadvantage is that it has high water absorption, which affects dimensional stability and electrical properties. Fiber reinforcement can reduce the water absorption of the resin, so that it can work under high temperature and high humidity.
Use
1111, 1101 fluidized bed process: powder diameter: 100um coating thickness: 350-1500um
1164, 2157 micro-coating process: Powder diameter: 55um Coating thickness: 100-150um
2158, 2161 Electrostatic spraying: Powder diameter: 30-50um Coating thickness: 80-200um
PA12-P40 P60 laser sintering rapid prototyping Particle size: 30~150um
Applications: Dishwasher baskets, nylon-coated buckles, auto parts coating, coil coating, industrial fabric coating, texture coating additives, metal surface coatings, air conditioner protective nets; fluidized bed, vibration plate. High-performance fine powder can produce highly elastic and wear-resistant texture coatings. It has the characteristics of smooth surface, bright color, good film elasticity, high mechanical strength, good adhesion, and at the same time has the characteristics of wear resistance, heat resistance, moisture resistance, rust resistance, aging resistance, etc. The material is non-toxic and harmless to the human body. Widely used in the coating of calendars, desk calendars, underwear hooks, sports equipment, wire surface coating, bridges, ships and other wires, pipes and engineering components.
Cleaning Application
Adding oil-absorbing materials such as organic bentonite or nylon powder to the cleanser, even if the excess cleanser is washed off, these raw materials remain on the surface of the skin and continue to function, so it is expected that the oily skin can control the skin to a certain extent Increased oil output to control the shine that typically reappears 3 hours after skin cleansing.
Particle Size
The significant difference between powder coatings and solvent-based coatings is that the dispersion medium is different. In solvent-based coatings, organic solvents are used as the dispersion medium; while in powder coatings, purified compressed air is used as the dispersion medium. The powder coating is in a dispersed state during spraying, and the particle size of the coating cannot be adjusted. Therefore, the fineness of powder particles suitable for electrostatic spraying is important.
Powder coatings suitable for electrostatic spraying should preferably have a particle size between 10 microns and 90 microns (ie >170 mesh). Powders with a particle size of less than 10 microns are called ultrafine powders, which are easily lost in the atmosphere, and the content of ultrafine powders should not be too much. It is worth noting here that the particle size of the powder is related to the thickness of the coating film. The particle size of the powder coating must have a certain distribution range to obtain a coating film with uniform thickness. If the thickness of the coating film is required to be 250 microns, the largest particle size of the powder coating should not exceed 65 microns (200 mesh – 240 mesh), and most powders should pass through 35 microns (350 mesh – 400 mesh). In order to control and adjust the size of powder particles, it should be able to be adjusted on the crushing equipment.
When the particle size of the powder exceeds 90 microns, the ratio of the charge to the mass of the particle is very small during electrostatic spraying, and the gravity of the large-particle powder soon exceeds the aerodynamic and electrostatic forces. Therefore, the large-particle powder has greater kinetic energy , It is not easy to adsorb to the workpiece.
Nylon powder is a versatile material that has a wide range of applications across various industries. From aerospace to consumer goods, nylon powder is preferred because of its strength, durability, and resistance to wear and tear. With the continued development of additive manufacturing technologies, the demand for nylon powder is expected to grow significantly in the coming years.
Military and Defense
Nylon powder is used in the military and defense industry to produce components such as gears, bearings, and other critical parts of military equipment. Nylon powder is preferred in this industry because it is tough, lightweight, and resistant to chemicals and heat.
Electrical and Electronics
Nylon powder is used in the electrical and electronics industry to produce components such as connectors, switches, and circuit breakers. Nylon powder is preferred in this industry because it is an excellent insulator and has high dielectric strength, meaning it can withstand high voltages without breaking down.
Consumer Goods
Nylon powder is used in the production of consumer goods such as toys, household appliances, and furniture. Nylon powder is preferred in this industry because it is tough, durable, and resistant to wear and tear.
Packaging
Nylon powder is used in the production of packaging materials such as films, bags, and pouches. Nylon powder is preferred in this industry because it is strong, flexible, and resistant to punctures and tears.
Textiles
Nylon powder is used in the production of textiles such as clothing, upholstery, and carpets. Nylon powder is preferred in this industry because it is strong, durable, and resistant to abrasion and chemicals.