Nylon Powder Electrostatic Spray Coating Process
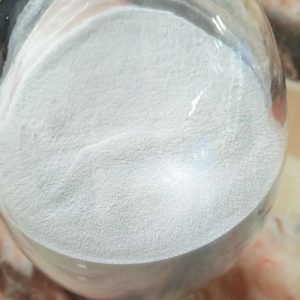
The electrostatic spray method utilizes the induction effect of a high-voltage electric field or the friction charging effect to induce opposite charges on the nylon powder and the coated object, respectively. The charged powder coating is attracted to the oppositely charged coated object, and after melting and leveling, a nylon coating is obtained. If the coating thickness requirement does not exceed 200 microns and the substrate is non-cast iron or porous, no heating is required for cold spraying. For powder coatings with thickness requirements greater than 200 microns or substrates with cast iron or porous materials, the substrate needs to be heated to around 250°C before spraying, which is called hot spraying.
Cold spraying requires nylon powder particles to have a diameter of about 20-50 microns. Sometimes, water mist can be sprayed into the powder to increase its ability to carry charges and reduce defects caused by powder loss before baking. Hot spraying requires nylon powder particles to have a diameter of up to 100 microns. Coarser particles can result in thicker coatings, but excessively coarse particles can hinder powder adhesion. During hot spraying, the substrate temperature decreases continuously, making it difficult to control the thickness, but the coating will not produce powder loss defects.
The electrostatic spraying process has a wide range of options for selecting workpiece sizes, especially for workpieces with different thicknesses, ensuring similar thicknesses. When the workpiece is not entirely coated or has a complex shape that cannot be immersed in a fluidized bed, the electrostatic spraying process has advantages. High-temperature, wear-resistant adhesive tape can be used to temporarily protect the uncoated parts. Generally, electrostatic spraying can achieve a thinner coating, such as between 150 microns and 250 microns. Additionally, the nylon coating obtained by electrostatic cold spraying has a low melting temperature, typically around 210-230°C for 5-10 minutes, good toughness, and low thermal degradation. The adhesion to the metal is better than other processes.
hi,do you have dip type nylon powder,instead of electrostatic spraying?
I do agree with all of the ideas you have presented in your post. They are really convincing and will certainly work. Still, the posts are too short for newbies. Could you please extend them a little from next time? Thanks for the post.