Fusion Bonded Epoxy FBE Powder Coat for 3LPE Pipeline
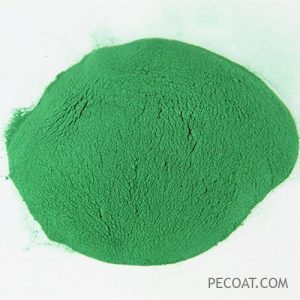
Fusion Bonded Epoxy (FBE) powder coating is commonly used as a corrosion protection coating for 3LPE pipelines. It is applied to the external surface of the pipeline to provide a durable and protective barrier against corrosion.
FBE powder coating is typically applied using electrostatic spray or fluidized bed methods. The powder is heated and melted onto the surface of the pipeline, forming a continuous and uniform coating. Once cooled, the FBE coating provides excellent adhesion and resistance to chemicals, moisture, and abrasion.
The 3LPE pipeline coating system consists of three layers: the FBE primer, an adhesive layer, and a polyethylene topcoat. The Fusion Bonded Epoxy primer acts as a bonding agent between the steel surface and the adhesive layer, ensuring good adhesion. The adhesive layer provides additional corrosion protection and serves as a bonding layer for the polyethylene topcoat.
PECOAT® jointly developed and produced high-performance Fusion Bonded Epoxy powder coating, which is mainly composed of special resins and finely formulated with excellent additives and specific ingredients. It has good compatibility with the copolymer adhesive in 3PE anti-corrosion for pipelines, and is used for coating or immersion processes to carry out operations and construction on steel pipe components. It not only has excellent corrosion resistance but also outstanding mechanical properties, making it suitable for various climate conditions worldwide.
Colors: Gray, blue, green, etc. can be customized.
Execution standards: GB/T 23257-2017 and SY/T 0315-2005.
Characteristics
- Uniform color, no agglomeration or lumping
- High bonding strength with anti-corrosion layer adhesive
- Superior cathodic peeling performance and dielectric strength
- Strong resistance to chemical corrosion such as acid, alkali
Powder Performance
Coating Performance
Application Method of Fusion Bonded Epoxy
- Remove Rust, Oil And Debris From The Surface Of The Steel:Shot blasting and sandblasting treatment to the Ss2.5 level specified in GB/T8923;Anchor pattern depth of 50-70um;Blow off the dust and abrasives on the surface of the steel.
- The preheating temperature of the anticorrosive parts should be controlled at 200-240℃, and the actual construction can be adjusted according to the on-site construction conditions.
- Use electrostatic spraying method for construction operation (voltage between 60-90kv, spraying distance between 150-200mm), coating thickness of 100-150um.
- The construction environment should be dry and clean.
- The epoxy powder should be opened and used as needed, and the remaining products should be sealed in time to avoid dust pollution and moisture in the air.
Package and Storage Of Fusion Bonded Epoxy
- Carton and inner sealed packing bag: 25kg/Box.
- Avoid exposure to the sun, rain, away from the fire, the temperature is ≤35℃ is appropriate.
- Stack height ≤5 layers to avoid pressure, ensure airtight, prevent moisture (relative humidity < 75%).
- Shelf life of 12 months.
Health, Safety and Environmental Protection
- During use, it is necessary to strengthen protection by wearing dust masks and goggles to prevent dust from entering the mouth and eyes.
- It must be used in a well-ventilated environment, and the dust concentration in the air must be less than 20g/cm3 to avoid explosions.
- Smoking is prohibited at the use site, and open flames are strictly prohibited. Fire extinguishers must be provided, and emergency plans must be prepared in advance.
- If inhaled or ingested, seek medical attention immediately.
- Residual waste cannot be reused and should be sent to a garbage station for centralized treatment.
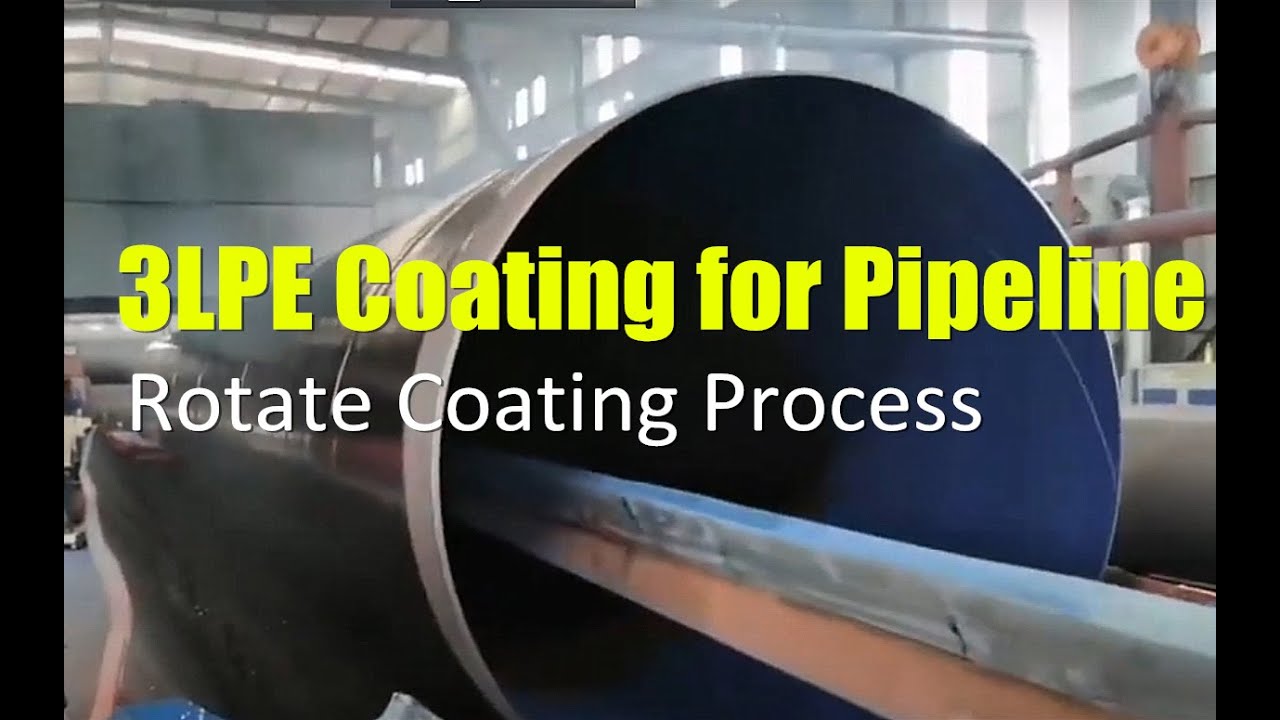