Dip Molding Technology and Its Application in Automobile
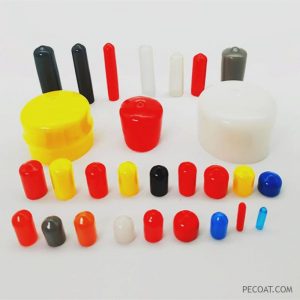
Engineers in the automotive industry are well-versed in techniques such as injection molding, press molding, electroplating, spraying, and other established molding methods. However, the plastic dip molding technology could be relatively unfamiliar to them as it has not been widely implemented in some developing countries, with a history of only nearly 30 years. Conversely, in developed regions like the United States and Europe, dip molding technology has been extensively developed since the Second World War, originally used for the protection of military components such as those found in automobiles and aircraft. This technology has a history of nearly 70 years.
Dip molding technology developed owing to the discovery of PVC plastisol material, a liquid sol material created from PVC plastic powder and plasticizer. This material was initially discovered in 1913 and its use became widespread in the Second World War.
Dip Molding Process
The processing process of dip molding is shown below:
The dipping molding process involves five main steps: preheating, dipping, curing, cooling, and demudding. After undergoing post-treatment (tail cutting), the product is considered a finished product. Finally, it undergoes sorting, packaging, and storage.
Preheating
The objective is to enable the liquid plastisol to adsorb onto the surface of the heated mold. Due to variations in mold size and plastisol type, the preheating temperature and time may differ. Generally, larger molds require higher temperature and longer time, while smaller molds experience lower temperature and shorter time. Moreover, the material and heat capacity of the mold, as well as the thickness and hardness of the product, can vary, necessitating different dipping temperatures and times. Therefore, it is essential to perform tests based on the specific circumstances to determine the optimal process parameters.
Dipping
The hot mold is immersed into the liquid plastisol at a speed of less than 10mm/s, and the mold lifting speed is less than 5mm/s. The dipping time is adjusted according to the size and thickness of the product, typically ranging from 1 to 60 seconds.
Curing (Plasticizing)
The objective is to guarantee that the product achieves complete hardening and assumes its final shape. The curing temperature and time should be adjusted according to the mold material, the volume size, and the desired hardness and thickness of the product. Typically, the curing temperature ranges between 200 and 350 degrees Celsius, while the plasticizing time spans from 10 to 90 seconds.
Cooling
The purpose is to improve mass production efficiency, cooling methods include water cooling and air cooling.
Demoulding
The demoulding method of plastisol impregnated products is generally pneumatic demoulding. In addition, no demoulding is required for dip coated products.
Plastisol Materials for Dip Molding
At present, there are three main types of liquid plastisol materials:
- Latex with water as a dispersion medium, such as natural latex, synthetic latex (nitrile rubber, polyisoprene rubber, polyurethane, etc.);
- Polymer solutions with solvents (xylene, tetrahydrofuran, dimethylacetamide, etc.) as dispersion media, such as polyurethane, liquid silicone rubber solution;
- Plasticizer sol (mainly refers to PVC plastisol ), that is, the liquid suspension sol prepared by plasticizer and PVC paste.
The requirements for the materials used in dipping equipment differ depending on the type of equipment and its intended application. This paper mainly introduces the material requirements for PVC plastisol. PVC plasticizer sol is distinct from the other two types of materials, as the dispersion medium is a plasticizer that remains non-volatile during the heating hardening process. It is compatible with the PVC paste plasticizer, resulting in a soft (rubber state) or semi-hard form of PVC material.Due to its simple processing, high efficiency (requiring no volatilization recovery device in the equipment process), low material cost, softness, and excellent electrical properties, PVC sol has become a widely used dipping material. It is widely utilized in various fields such as power (busbar), electrical parts, daily necessities, optical fiber communication protection, and medical health protection. In the United States, Europe, Japan, and India, the promotion of PVC plastic technology is more mature. China is a powerhouse in PVC production and export; however, its PVC plastisol technology started late.
With the advancement of material technology and the expansion of application fields, the functions of PVC plastisol materials have gradually increased, mainly including flame retardant, UV radiation resistance, insulation, food grade, biocompatible (medical), phthalate-free, oil-resistant. Among them, PVC plastisol containing phthalates was the first to be restricted by Europe (phthalates will interfere with male endocrine, increase the probability of female breast cancer), and gradually regularized, so as to limit the use of some conventional plasticizers, the EU REACH/RoHS regulations are becoming more and more stringent.
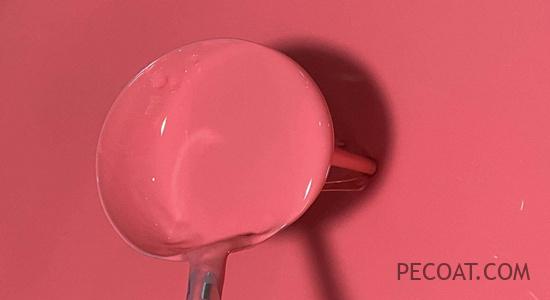
The Application of Dip Molding Technology in Automobiles
Plastisol material in the automotive industry the earliest application of Ford motor in 1959, China began to develop automotive PVC plastisol material in the 1980s, the general consumption of 6-10kg, accounting for about 35% of the total amount of glue. Such as car chassis protective coatings and sealing materials for different parts of the car. A car from the wheel to the smallest screw, there are more than 10,000 protective parts, these parts are mainly plastic coatings, protective caps, jackets, bushings and so on. The accessories have different shapes and flexible structural design, which is most suitable for production by dipping technology.
Automotive Wiring Harness Sheath
The plastic sheath is used for automotive wiring harness, specifically for the protection of automotive wiring harness plug terminals, with insulation, flame retardant, temperature resistance, environmental protection functions.
Battery Discharge Protection
The plastic dip molding technology is used for the insulation protection of battery joints and copper bars of new energy power batteries. It has the characteristics of flexible structure design, fast development cycle and customization.
Automobile Wire Clamp and Pole Protection
The impregnation technology is used for the protection of automobile wire clamp and rod parts, which can form flexible protection and anti-corrosion and dust-proof functions.